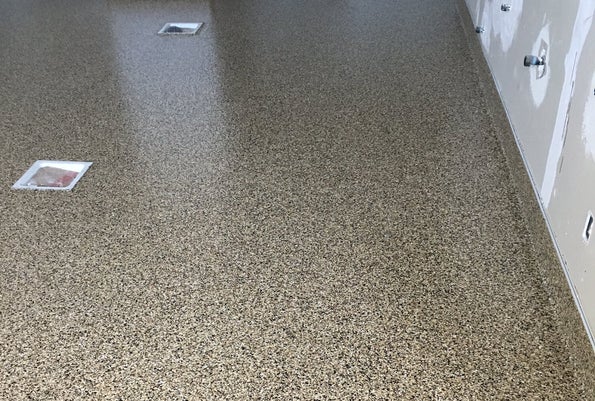
The Value of Resinous Epoxy Floors for Your Home or Business
Choosing the right flooring solution is more than just another expense in your construction or renovation budget—it’s an investment in your home or business’s long-term value and success. The flooring you install must be durable, cost-effective, and suited to the unique needs of your installation.
Are Resinous Epoxy Floors Worth the Investment?
In any flooring installation, controlling costs is crucial. While it’s tempting to choose the cheapest flooring option, a low initial price may lead to higher long-term costs due to frequent repairs and replacements. Resinous flooring solutions, like epoxy coatings, provide exceptional durability and protection, ultimately reducing maintenance expenses over time.
A standard epoxy floor is one of the most affordable and long-lasting flooring solutions available. Costs will vary depending on the specific epoxy formulation, as well as any necessary additives such as chemical resistance, antimicrobial properties, or slip resistance. While these customizations may increase the initial investment, they contribute to cost savings in the long run by reducing the need for repairs and ensuring compliance with industry regulations.
The Cost-Effectiveness of Resinous Flooring for Commercial and Industrial Spaces
Selecting the right resinous flooring system means evaluating various factors, including material selection, installation techniques, and initial preparation. Properly installed epoxy and other resin-based flooring systems offer outstanding resistance to damage, making them ideal for high-traffic areas, mobile workspaces, and environments exposed to heavy equipment.
Compared to traditional flooring materials like tiles, vinyl, or unfinished concrete, resinous coatings provide superior longevity and performance. But with multiple types of resinous flooring available, how do you determine which is the best fit for your business?
Resinous Flooring Installation Costs
Every resinous floor starts with a concrete base, which must be properly cleaned and prepared before applying the resin. Moisture and debris can compromise the integrity of the floor, making this preparation phase a critical step in the installation process.
The total cost of installation depends on factors such as:
-
The type of resin used (epoxy, urethane, or methyl methacrylate)
-
The complexity of the installation
-
Any necessary surface preparation and repairs
-
The size of the installation area
Partnering with an experienced and highly qualified epoxy flooring contractor ensures that your flooring is installed correctly the first time, reducing the likelihood of early failures or the need for costly rework.
Key Considerations When Estimating Epoxy Flooring Costs
Several factors influence the final cost of an epoxy flooring system, including:
-
Durability and Damage Resistance
Floors endure constant wear and tear, from heavy equipment and foot traffic to dropped tools and chemical spills. While some cheaper flooring materials may seem appealing, they often require frequent repairs. A high-quality resinous floor coating will better withstand these challenges, providing greater long-term value. -
Maintenance and Cleanliness
Regular maintenance is essential for extending the life of any flooring system. Dirt and debris can degrade some flooring materials over time, leading to unsightly damage. Epoxy flooring, however, is easy to clean and maintain, making it a preferred option for industries that require high levels of sanitation, such as food processing and pharmaceuticals. -
Chemical Resistance
Businesses handling hazardous chemicals must ensure their flooring can withstand exposure without degrading. Epoxy and urethane coatings offer excellent resistance to acids, solvents, and harsh cleaners, preventing damage and ensuring workplace safety. -
Aesthetic and Design Preferences
Resinous flooring is available in a variety of finishes, including decorative flakes, metallic coatings, and custom color blends. This allows businesses to choose a design that aligns with their branding and operational needs.
Comparing Epoxy, Urethane, and MMA Flooring Costs
Epoxy Flooring
-
One of the most cost-effective options, starting as low as $2.50 per square foot for large-scale installations.
-
Provides excellent durability but is slightly brittle and susceptible to impact damage.
-
Requires a curing period of 48-72 hours, which may impact operational downtime.
Urethane Flooring
-
More expensive than epoxy, with costs ranging from $6-$19 per square foot depending on the project size.
-
Highly resistant to UV exposure, making it ideal for spaces with significant natural light.
-
More flexible than epoxy, allowing it to withstand impact and temperature fluctuations better.
Methyl Methacrylate (MMA) Flooring
-
Higher initial cost, but rapid installation and curing (usable within hours) minimize business disruption.
-
Aesthetic appeal makes it a great choice for areas with customer foot traffic.
-
A balance between the durability of epoxy and the flexibility of urethane.
Why Choose ProResin Flooring Solutions?
At ProResin Flooring Solutions, we specialize in custom-engineered commercial and industrial flooring systems designed to maximize durability, safety, and cost-effectiveness. With our expert installation process and commitment to quality, we help businesses achieve long-lasting flooring solutions tailored to their unique needs.
Contact us today for a free consultation and discover how we can help you value-engineer the perfect flooring solution for your business.
Add comment
Comments